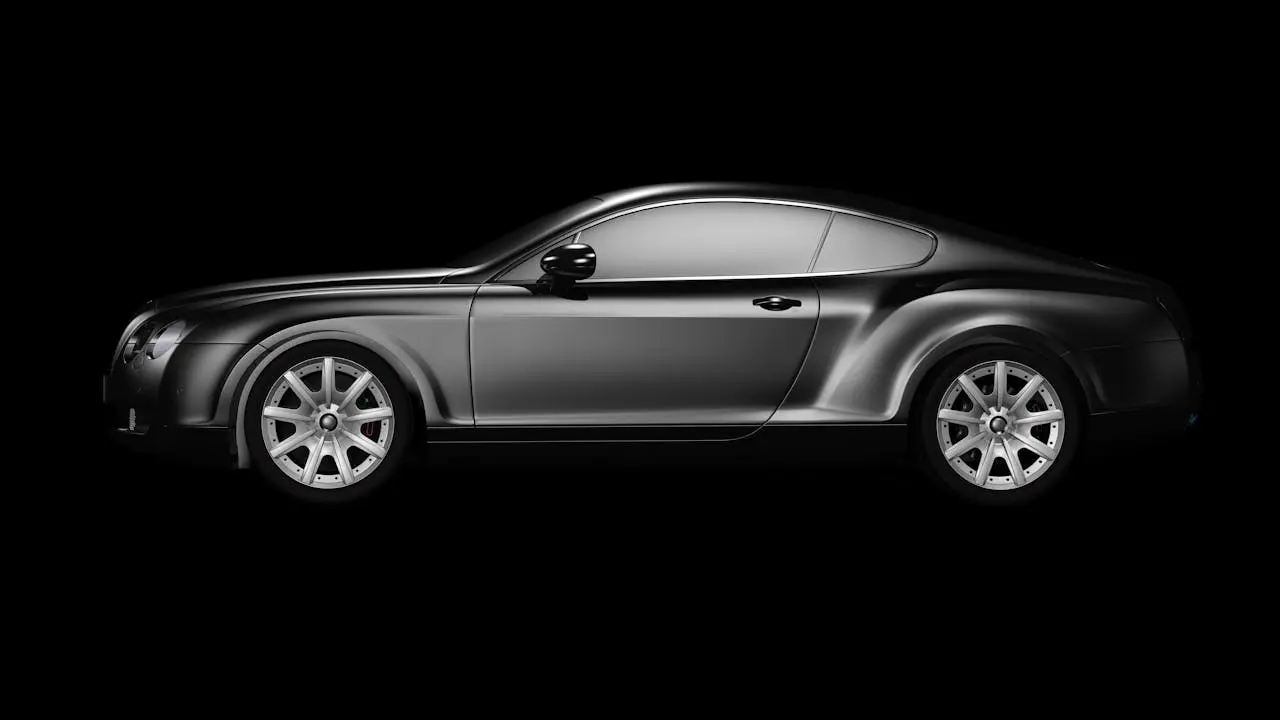
The “Automotive Integrated Die Casting Industry Report, 2024” has been added to ResearchAndMarkets.com’s offerings. This report provides a comprehensive analysis of the current state of the integrated die casting industry, examining the product layouts of OEMs and suppliers, and forecasting future trends in the industry.
Integrated die casting has gained significant traction, with nearly 20 OEMs adopting this technology. Notable advancements have been made in the upstream supply chain, including die casting machines, molds, and non-heat-treatable materials.
Super-large Die Casting Machines:
The tonnage of super-large die casting machines has increased dramatically, from 6000T to 16000T, with development underway for 20000T machines. Large die casting machines are crucial for automotive integrated die casting, generally requiring machines with over 6000T clamping force. Currently, only a few manufacturers, such as IDRA, Brown, Boveri & Cie, L.K. Technology, Haitian Die Casting, and YIZUMI, produce these machines.
In October 2023, L.K. Technology unveiled a 16000T super-large intelligent die casting unit, the largest in the world, capable of covering class A0-C and SUV models. Companies like Tesla, L.K. Technology, and Haitian Die Casting are now developing machines exceeding 20000T. In June 2023, Haitian Die Casting and Chongqing Millison Technologies announced their joint development of 20000T machines. By December 2023, L.K. Technology and Neta Auto signed a strategic agreement to develop >20000T equipment for class B vehicle chassis.
Integrated Die Casting Molds:
The weight of integrated die casting molds now exceeds 250 tons. Before 2023, only a few Chinese companies, like GZDM Technology and Ningbo Sciveda Mould, could produce ultra-large molds. Now, companies like Chongqing Millison, Rayhoo Motor Dies, and Ningbo Xinlin Mould Technology can also produce these molds. Although HLGY and Qixin Mould have not yet mass-produced products, they are actively developing capabilities.
Significant technological breakthroughs have occurred in mold R&D. For instance, ZDM (Zhenzhi) Machinery & Mould, which produced 50T molds in 2019, developed an 80-ton body structure mold for a new energy vehicle company. By May 2023, ZDM created a 250-ton integrated body structure mold for front and rear chassis.
Non-heat-treatable Materials:
Chinese manufacturers have advanced in non-heat-treatable materials through patent licensing, independent R&D, and collaborations with universities and automakers. Alcoa and Rheinfelden pioneered these materials in the 1990s, while Lizhong Group entered the Chinese market in 2020. Today, numerous Chinese entities, including Shanghai Yongmaotai Automotive Technology and Hubei Xinjinyang, hold patents for these materials.
In August 2023, Xiaomi Automobile secured a patent for its self-developed alloy material, “Xiaomi Titans Metal.” In November 2022, ZEEKR and Suzhou Huijin Smart Technology Co., Ltd. introduced “Xianjing,” a new non-heat-treatable high-strength aluminum alloy material.
Application in Vehicle Bodies:
Since Tesla’s use of a 6000T die casting machine for the Model Y’s rear underbody in 2020, other Chinese automakers like NIO, Xpeng, and Li Auto have adopted integrated die casting. This technology is now used in various vehicle parts, including rear underbodies, front cabins, and battery trays.
As of April 2024, integrated die casting was in mass production for several components:
- Rear Underbody: Models like NIO ET5, Xiaomi SU7, and ZEEKR 009/007 feature mass-produced integrated die cast rear underbodies.
- Front Cabin: Automakers produce front cabin components for models such as the new NIO ES8 and Xpeng G6/X9.
- Middle Integrated Die Cast Parts: ZEEKR 001 FR’s middle integrated parts are in mass production.
- Battery Tray: L.K. Technology has mass-produced the largest integrated battery tray globally, measuring about 21801500110.
By 2027, integrated die casting is expected to extend to battery case upper covers, middle floors, and underbody assemblies. Tesla, FAW, and Xpeng have plans to implement large die cast parts, aiming to reduce the weight and manufacturing costs of vehicle components significantly. For instance, Tesla plans to replace a 370-component underbody assembly with 2-3 large die cast parts by 2025, reducing weight by 30% and manufacturing cost by 40%.