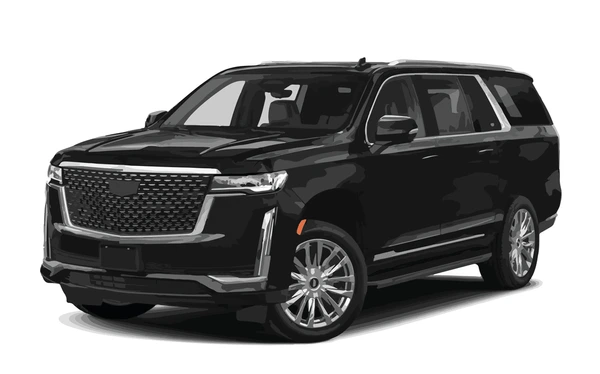
Cadillac Elevates Craftsmanship and Innovation in CELESTIQ with 3D-Printed Precision
General Motors (GM) has long been at the forefront of automotive innovation, from pioneering electric vehicles to embracing cutting-edge design processes. One of the most transformative technologies GM has embraced in recent years is additive manufacturing—commonly known as 3D printing. Initially adopted as a tool for creating prototype parts to support the engineering and design process, GM is now leveraging 3D printing well beyond the development stage. Today, this technology is being used to produce functional components in actual production vehicles, helping streamline development timelines and unlock new possibilities in vehicle design.
At the heart of this advancement is Cadillac’s flagship ultra-luxury electric sedan, the CELESTIQ. Positioned as a halo vehicle and a bold expression of Cadillac’s return to its “Standard of the World” reputation, the CELESTIQ not only showcases premium materials, craftsmanship, and personalization—it also embodies GM’s leap forward in manufacturing with more than 130 3D-printed components integrated into the final vehicle.
A Bespoke Vision for the Future of Luxury
The Cadillac CELESTIQ is unlike any vehicle in the brand’s modern lineup. Hand-built to order, each vehicle is custom-commissioned for its buyer, with meticulous attention to detail and advanced manufacturing techniques guiding the production process. For such a one-of-a-kind vehicle, traditional manufacturing approaches were not sufficient. The flexibility, precision, and material efficiency offered by additive manufacturing made it the ideal solution for developing highly customized parts that meet both aesthetic and structural requirements.
One standout example of 3D-printed innovation in the CELESTIQ is its steering wheel center trim bezel—an elegant component that covers the front face of the steering wheel and frames the embedded control switches. This part is not only visually striking with a refined, seamless surface—it also holds the distinction of being GM’s largest 3D-printed metal production component to date.
This component is produced using metal laser powder bed fusion (LPBF) technology, one of the most advanced forms of additive manufacturing. LPBF builds parts layer by layer using a laser to melt and fuse powdered metal. This approach enables engineers to design and produce geometries that would be difficult or even impossible to fabricate using traditional casting or machining processes. The result is a strong, intricately detailed component that delivers both function and aesthetic excellence.
Design Freedom Meets Structural Integrity
According to Brennon White, GM technical specialist for advanced manufacturing production applications, the CELESTIQ project provided a unique opportunity to showcase the full potential of additive manufacturing in a low-volume, high-luxury production setting. White, who has spent over 14 years working in the field of additive manufacturing, played a pivotal role in evaluating and implementing 3D printing solutions across CELESTIQ’s complex component list.
“We wanted the part to be metal, to match the high-end aesthetic and feel of the vehicle,” White explains. “We explored several production methods, but additive stood out because it could deliver the kind of intricate, compact, and refined structure we needed.”
One of the most groundbreaking applications of 3D printing in CELESTIQ is a seatbelt guide loop that is not only visually polished but also plays a vital safety role. This component represents GM’s first use of a 3D-printed metal part in a functional safety system. Its development was recognized by the Metal Powders Industry Federation in 2024 with the Award of Distinction in the Automotive—Electric Vehicle Category, highlighting the industry’s growing acceptance of 3D printing for mission-critical vehicle components.
“None of the finishes we could find through conventional means met the luxury benchmark we set for CELESTIQ,” says White. “By using additive manufacturing, we were able to consolidate what would have traditionally been multiple parts into a single, seamless piece. The result is a design that is both structurally superior and aesthetically exquisite.”
From Racing Pedigree to Production Line
CELESTIQ is not the first GM vehicle to benefit from the capabilities of 3D printing. The technology made its production debut with Cadillac’s V-Series Blackwing models, where select components such as the gear shifter medallion were created using additive methods. In the world of motorsports, GM’s racing teams, including Cadillac Racing, have leveraged 3D-printed parts for years—taking advantage of the rapid iteration and customization that the technology affords.
However, CELESTIQ represents a turning point in how comprehensively additive manufacturing is being applied in a production vehicle. From decorative elements like console accents and window switch bezels to structural and interior subcomponents, CELESTIQ includes the highest number of 3D-printed parts of any GM production vehicle to date.
The Additive Industrialization Center: A Manufacturing Powerhouse
GM’s leadership in additive manufacturing is anchored at the Additive Industrialization Center (AIC), located at its Global Technical Center in Warren, Michigan. Opened in late 2020, the 15,000-square-foot facility houses more than 20 state-of-the-art 3D printers capable of producing both polymer and metal parts. The AIC functions as GM’s hub for additive innovation, experimentation, and production scaling.
Most of the parts that end up in CELESTIQ begin their life at the AIC, where GM engineers and designers validate designs and test manufacturing feasibility. Once proven, the parts can either be produced in-house for low-volume needs or transferred to qualified suppliers for scaled production.
The AIC has not only become a launchpad for vehicle innovation but also a model for how additive manufacturing can coexist alongside traditional production systems in the automotive sector.
Economic Viability and Engineering Strategy
While additive manufacturing offers exceptional design freedom and functional benefits, GM remains focused on ensuring that every part produced via 3D printing also makes economic sense. As White points out, the decision to use additive manufacturing is always grounded in practicality.
“When we evaluate a component for additive, we ask two main questions,” he says. “‘Can it meet the functional requirements?’ and ‘Does it make sense economically?’ If the answer to both is yes, then additive is the right path forward. That’s exactly how we approached CELESTIQ.”
This thoughtful strategy is what allows GM to continue expanding the scope of additive manufacturing without compromising quality, safety, or cost-effectiveness. For CELESTIQ, the unique demands of low-volume, personalized luxury production created the perfect environment for additive solutions to thrive.
Redefining Automotive Craftsmanship
Through CELESTIQ, GM and Cadillac are demonstrating that advanced technologies like 3D printing can elevate—not replace—craftsmanship. Each part tells a story of innovation and intention, whether it’s a hidden bracket, a sculptural interior touchpoint, or a safety-critical structural piece. Additive manufacturing is not only helping engineers solve complex problems but also empowering designers to dream bigger and deliver more for customers who demand the extraordinary.
As the automotive industry continues its transition toward electrification, digitalization, and customization, the role of technologies like additive manufacturing will only expand. And with CELESTIQ, Cadillac is proving that the future of luxury lies at the intersection of artisanal excellence and high-tech precision.