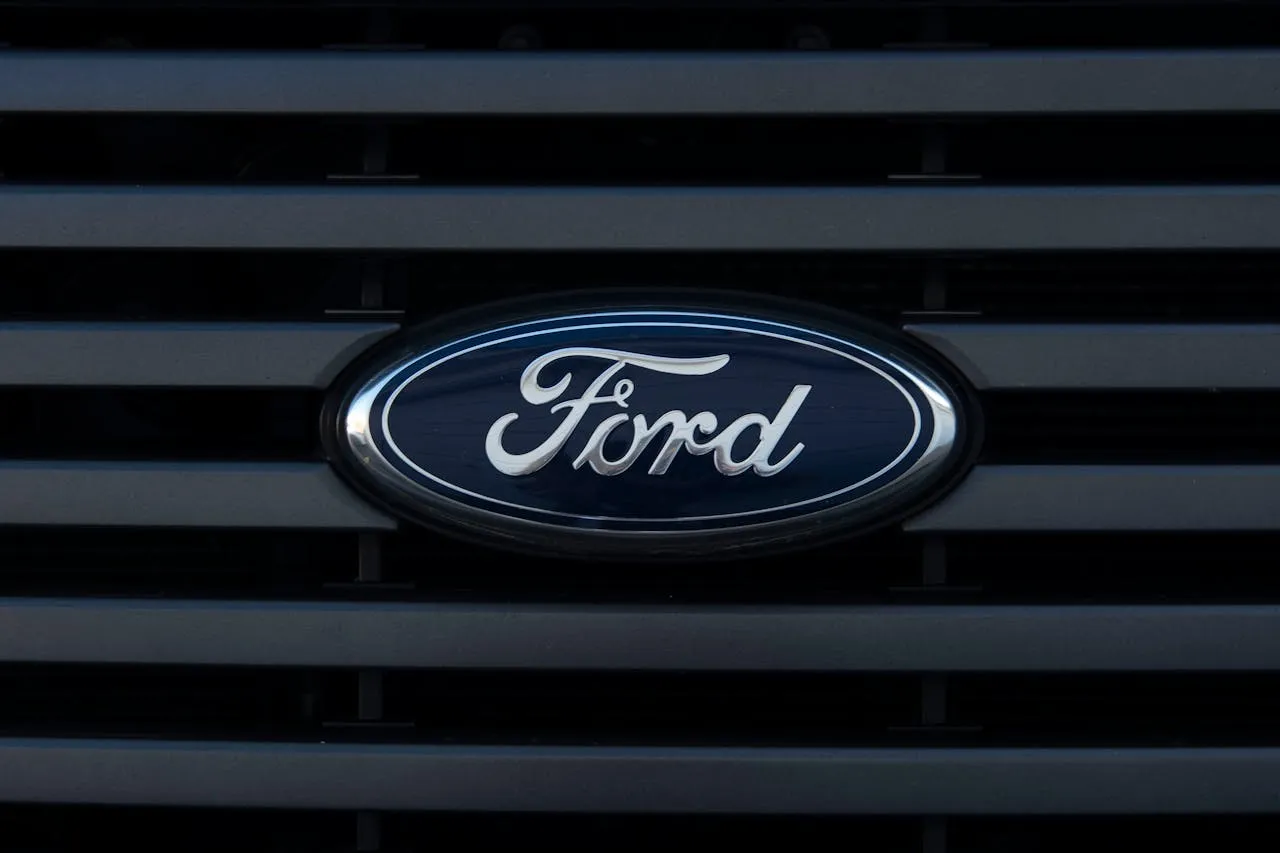
Ford Otosan Implements Quantum Technology to Optimize Vehicle Production
Quantum computing is rapidly evolving from an experimental technology to a practical tool that is transforming industries. One of the most compelling real-world applications has emerged in the automotive manufacturing sector, where production efficiency is paramount. Ford Otosan, a joint venture between Ford Motor Company and Koç Holding in Turkey, has successfully integrated quantum computing into its vehicle manufacturing process. By leveraging D-Wave’s annealing quantum computing technology, Ford Otosan has enhanced its production sequencing, leading to significant improvements in efficiency, flexibility, and overall throughput.
The Challenges of Vehicle Manufacturing
Ford Otosan is the global leader in manufacturing Ford Transit vehicles, one of the most customizable commercial vehicle lines available. With over 1,500 variants in production, managing production sequencing is a highly complex task. Unlike producing identical items in a continuous sequence, manufacturing customized vehicles requires frequent adjustments, which can introduce inefficiencies.
The core challenge lies in optimizing production sequences while maintaining high productivity. A well-sequenced manufacturing process minimizes disruptions, maximizes throughput, and ensures that physical and workforce constraints across the body shop, paint shop, and assembly line are met. Traditional computing methods, while effective, struggle with the complexity and scale of such optimization problems.
Quantum Computing’s Role in Production Optimization
To address these challenges, Ford Otosan collaborated with D-Wave, a leader in quantum computing systems, software, and services. Together, they developed a hybrid-quantum application that optimizes production sequencing, reducing scheduling times and improving overall efficiency.
D-Wave’s hybrid solvers, accessible through the Leap™ quantum cloud service, allowed Ford Otosan to decrease the time required to schedule 1,000 vehicles from 30 minutes to less than five. This dramatic reduction in scheduling time enables Ford Otosan to respond rapidly to changes in demand and auto part availability, reducing downtime and improving operational flexibility.
Ziya Dalkılıç, a data scientist at Ford Otosan, emphasized the importance of maintaining the highest standards in production efficiency:
“It is imperative that Ford Otosan maintains the highest standards of production processes and efficiencies to meet customer demand. Working with D-Wave’s technology, we’ve built and now deployed a quantum optimization application that goes beyond what we were able to achieve with a purely classical computing approach.”
Dr. Alan Baratz, CEO of D-Wave, highlighted the transformative potential of quantum computing in manufacturing:
“Production scheduling demands meticulous planning and agile responses, and classical computing methods can often struggle to keep up with the manufacturing industry’s growing scale and complexity. For manufacturers on the leading edge of innovation—such as Ford Otosan—D-Wave’s quantum computing technology has proven capable of finding better solutions to complex, real-world problems than classical computing alone. We’re thrilled to see this application move into production and help Ford Otosan realize the powerful benefits of quantum.”
Benefits of Quantum-Optimized Scheduling
By implementing quantum-enhanced scheduling, Ford Otosan has achieved several key operational benefits:
- Reduced Scheduling Time: The time required to sequence vehicle production has been cut dramatically, from 30 minutes to under five, improving responsiveness to shifting market conditions.
- Improved Manufacturing Efficiency: The optimization of production sequences has led to better throughput and minimized inefficiencies, reducing the frequency of unplanned maintenance.
- Enhanced Flexibility: The system allows for rapid adaptation to changes in demand and supply chain conditions, mitigating delays and disruptions.
- Increased Peak Production Throughput: By streamlining scheduling, Ford Otosan anticipates higher vehicle production per hour, reclaiming previously lost manufacturing time.
- Scalability: Plans are in place to expand quantum scheduling optimization beyond the initial production line to additional body shops, paint shops, assembly lines, and buffer zones.
Expanding Quantum Optimization Across the Manufacturing Process
Ford Otosan’s successful deployment of quantum-enhanced scheduling is only the beginning. With the initial results proving the efficacy of the technology, the company plans to integrate quantum computing into other aspects of its manufacturing process. This expansion will include:
- Paint Shops: Optimizing painting sequences to reduce time, minimize waste, and improve efficiency.
- Assembly Lines: Enhancing worker scheduling and material flow to maximize productivity.
- Buffer Zones: Managing inventory in staging areas to ensure a smoother transition between manufacturing phases.
These expansions will further embed quantum computing into the core of Ford Otosan’s operations, setting a precedent for other manufacturers looking to harness quantum technologies.
The Future of Quantum Computing in Automotive Manufacturing
Ford Otosan’s pioneering work with D-Wave serves as a compelling case study in the application of quantum computing to real-world industrial challenges. As the technology matures, other automakers are likely to follow suit, seeking to optimize their own production processes. Quantum computing holds immense potential for:
- Supply Chain Optimization: Reducing bottlenecks and improving logistics efficiency.
- Material Usage Optimization: Minimizing waste and improving sustainability in manufacturing.
- Predictive Maintenance: Identifying potential issues before they cause downtime, reducing maintenance costs.
Ford Otosan’s adoption of quantum computing underscores its commitment to innovation and operational excellence. By taking a forward-thinking approach, the company has positioned itself at the forefront of a technological revolution that is poised to reshape automotive manufacturing.
Ford Otosan’s successful deployment of D-Wave’s quantum computing technology marks a significant milestone in automotive manufacturing. By optimizing production sequencing, reducing scheduling times, and enhancing operational flexibility, Ford Otosan has demonstrated the real-world impact of quantum computing. As quantum technology continues to evolve, its applications in manufacturing will only grow, paving the way for a new era of efficiency and productivity in the automotive industry.
To learn more about Ford Otosan’s quantum application, visit their submission to the World Economic Forum’s Quantum Application Hub or explore D-Wave’s website for insights into how quantum optimization is transforming industries today.