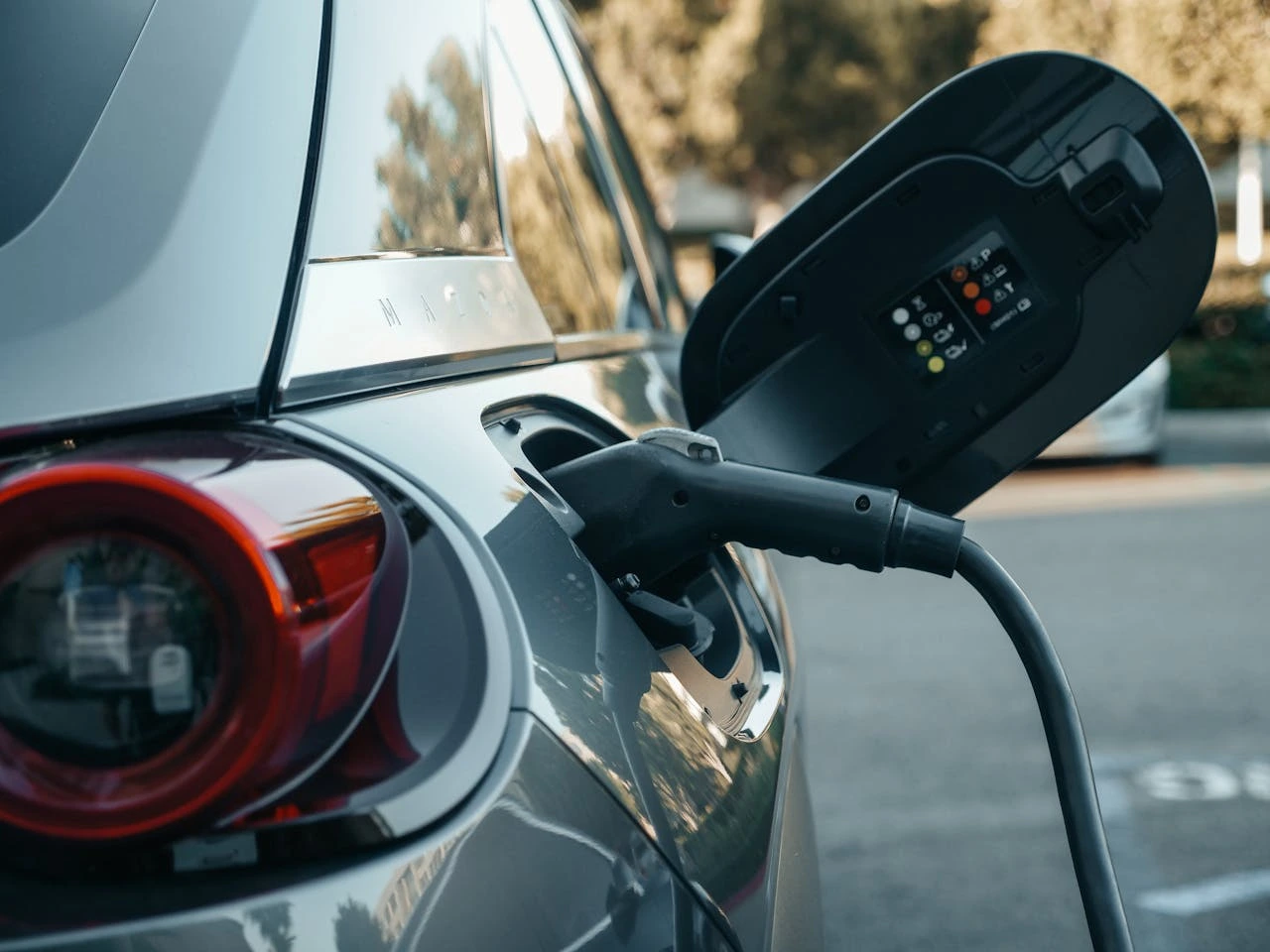
Mercedes-Benz has opened Europe’s first battery recycling plant featuring an integrated mechanical-hydrometallurgical process, located in Kuppenheim, southern Germany. This marks a significant step towards sustainable raw material usage, with an expected recovery rate exceeding 96%, and a net carbon-neutral operation. The plant is capable of recycling enough materials to produce over 50,000 new battery modules annually. This multi-million euro investment reinforces Mercedes-Benz’s commitment to creating a circular economy in the battery sector and supporting value creation in Germany.
The facility, developed in collaboration with technology partner Primobius and leading research institutions, enables Mercedes-Benz to close the battery recycling loop, becoming the first automaker to do so with its own in-house facility. The new plant aims to recover valuable raw materials like lithium, nickel, and cobalt, which will be repurposed for new batteries in future electric Mercedes-Benz vehicles. This milestone aligns with the company’s ambition to reduce reliance on primary resources.
At the opening ceremony, attended by Federal Chancellor Olaf Scholz and Baden-Württemberg’s Environment Minister Thekla Walker, Mercedes-Benz underscored its leadership in advancing sustainable mobility and resource conservation. Scholz emphasized that battery recycling is crucial for achieving climate goals, positioning the circular economy as both a growth driver and key to sustainable automotive production.
The plant uses a cutting-edge process that involves shredding and sorting materials such as plastics, copper, aluminum, and iron, followed by a hydrometallurgical process to extract critical metals from the battery’s active materials. This method is more energy-efficient than traditional pyrometallurgy, operating at lower temperatures (up to 80°C) and generating less waste. The recycling plant is powered entirely by green electricity, with solar panels installed on the roof.
With an annual capacity of 2,500 tonnes, the Kuppenheim facility will provide materials for more than 50,000 battery modules used in new Mercedes-Benz electric vehicles. The knowledge gained here will also help scale up battery recycling efforts in the future.
In line with its holistic approach to sustainability, Mercedes-Benz has embedded circular thinking into its entire battery value chain. This includes designing batteries for reuse, offering reconditioned batteries for spare parts, and giving second-life applications to batteries through large-scale energy storage systems. The company’s net carbon-neutral battery production operates across three continents, further supporting its sustainable business strategy.
At the opening, Jörg Burzer, Member of the Board of Management at Mercedes-Benz, highlighted that this plant strengthens the brand’s European production network, while Thekla Walker praised the initiative for reducing resource dependency and promoting resilience in raw material availability, reinforcing Baden-Württemberg’s leadership in innovative, sustainable technologies.