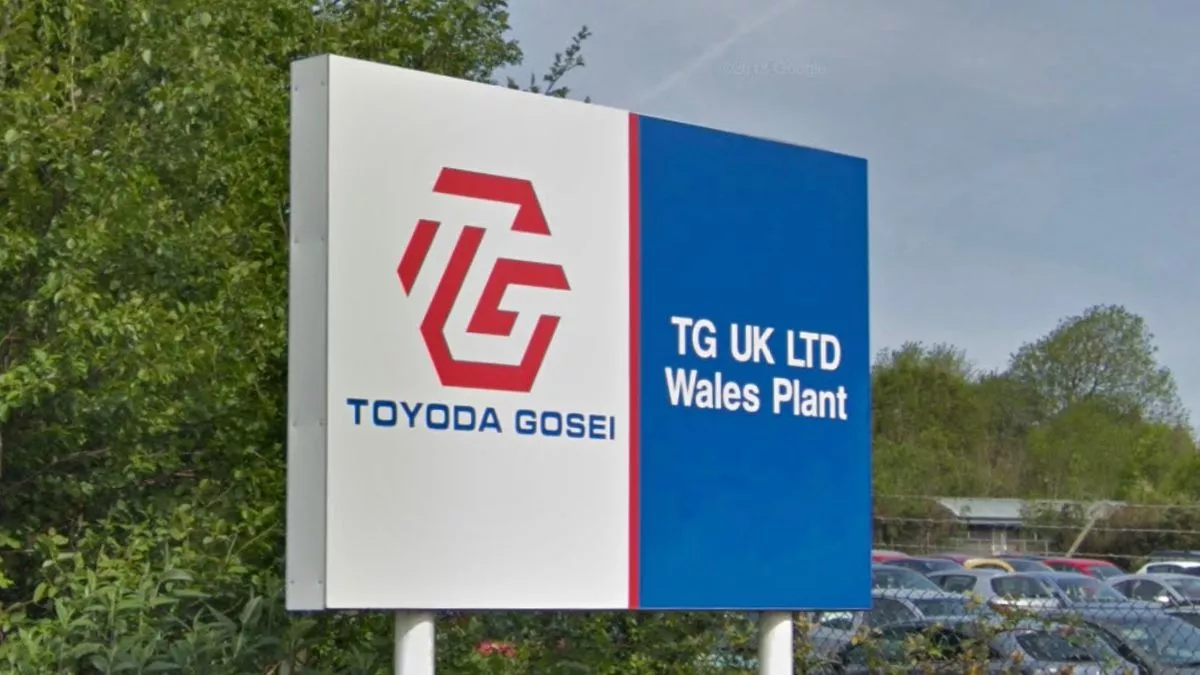
Tyoda Gosei Pioneers Horizontal Recycling Technology to Advance Sustainable Automotive Manufacturing
Toyoda Gosei a leading global supplier of automotive components, has announced the successful development of an innovative horizontal recycling technology that allows for the reuse of high-quality plastic from end-of-life vehicles (ELVs). This breakthrough not only helps meet the growing demand for sustainable materials in the automotive sector but also addresses increasingly stringent environmental regulations—particularly in regions such as Europe, where recycled content requirements are set to become mandatory for new vehicles starting in 2031.
This landmark achievement represents a significant step forward in circular economy practices within the automotive industry. Toyoda Gosei’s horizontal recycling initiative enables the use of recycled polypropylene plastic derived from ELVs in new automotive components—most notably, in interior parts such as glove boxes. The company’s efforts will initially be implemented in vehicle models such as the Toyota Camry, which has been manufactured in Japan and distributed globally, including in Europe, since 2024.
Overcoming Longstanding Recycling Challenges
Historically, recycling plastic from ELVs has been a complex challenge for the automotive industry. Plastics recovered from scrapped vehicles often contain impurities and degradation that compromise their mechanical properties. As a result, most ELV plastics have been subjected to thermal recycling—where waste plastic is incinerated to recover heat—or downcycled for use in products with lower performance requirements. Both approaches limit the potential for true circularity and do little to reduce the industry’s environmental footprint.
Toyoda Gosei has now broken this cycle. By developing an advanced material modification technology, the company has succeeded in processing ELV-derived polypropylene so that it meets the high-performance requirements for automotive interior parts. Remarkably, the company has achieved this performance standard even with a recycled content of 50% ELV plastic—a first-of-its-kind accomplishment in the automotive sector.
In collaboration with Isono Co., Ltd., a partner specializing in plastic material recovery, Toyoda Gosei ensures that raw materials used in the recycling process meet the necessary quality benchmarks. The resulting recycled plastic exhibits physical properties—such as impact resistance and durability—that match those of virgin material. This ensures the safety, performance, and longevity of the parts manufactured from the recycled material.
A First in Automotive Interior Applications
The application of this recycled material in glove boxes is particularly noteworthy. These components require a high degree of impact resistance to withstand the physical stresses encountered during regular vehicle operation. Until now, recycled plastics were rarely used in such demanding applications due to performance limitations. Toyoda Gosei’s achievement marks the first time globally that a recycled plastic containing such a high proportion of ELV content has been successfully used in parts requiring significant mechanical strength.
The glove boxes made with this recycled material have been introduced in the latest Toyota Camry models sold in Europe and other international markets. This implementation not only validates the material’s quality but also sets a new precedent for future applications across other vehicle components
Advancing CO2 Reduction Goals Through Horizontal Recycling
The environmental benefits of Toyoda Gosei’s new horizontal recycling technology are substantial. According to calculations based on the IDEA (Inventory Database for Environmental Analysis) platform developed by Japan’s National Institute of Advanced Industrial Science and Technology, using the new recycled plastic in parts manufacturing can reduce carbon dioxide emissions by up to 40%. The actual reduction varies depending on product size and other manufacturing variables, but the overall impact is a meaningful contribution to automotive sustainability.
Unlike traditional downcycling, where recycled materials are relegated to lesser applications, horizontal recycling refers to the process of reusing materials in the same type of product from which they were originally sourced. This allows manufacturers to close the material loop, conserving resources and minimizing waste. For Toyoda Gosei, horizontal recycling is a key strategy in its broader commitment to decarbonization and sustainable development.
A Strategic Fit with Long-Term Business Goals
This development is closely aligned with Toyoda Gosei’s 2030 Business Plan, which emphasizes environmental responsibility and the creation of a circular economy across all business operations. As part of its medium- to long-term strategy, the company is prioritizing innovation in material technologies that support decarbonization, resource efficiency, and regulatory compliance.
With environmental regulations tightening across global markets, particularly in Europe under directives such as the revised End-of-Life Vehicles (ELV) regulation, automotive manufacturers and suppliers are under increasing pressure to incorporate recycled materials into their products. The European Commission’s latest proposals would require automakers to ensure that a certain percentage of the plastic used in new vehicles comes from recycled sources, beginning in 2031. Toyoda Gosei’s proactive approach positions the company as a forward-thinking leader prepared to meet these demands well ahead of schedule.
Expanding Applications and Continuous Improvement
Building on this success, Toyoda Gosei plans to extend the use of its high-quality recycled plastics to a broader range of automotive components, including those with complex shapes or surface finishes. These may include decorative interior trim pieces, structural brackets, and even exterior panels, depending on performance requirements.
Moreover, the company is investing in continuous improvement of its recycling processes. Ongoing research and development efforts are focused on enhancing material properties, improving energy efficiency during processing, and refining supply chain logistics for plastic recovery and preprocessing.
Toyoda Gosei also intends to collaborate more closely with vehicle manufacturers, recycling firms, and government bodies to establish industry-wide standards and practices that support the growth of horizontal recycling. These partnerships will be critical to scaling the technology, improving consumer awareness, and making recycled materials the norm rather than the exception.
A Model for Sustainable Innovation in the Automotive Sector
Toyoda Gosei’s new horizontal recycling technology represents a model for sustainable innovation in the automotive industry. By addressing both the technical and environmental challenges associated with plastic recycling, the company has laid the foundation for a new generation of eco-conscious vehicle components.
As the world transitions toward a greener and more resource-efficient future, solutions like these will be instrumental in redefining the relationship between manufacturing and the environment. Toyoda Gosei’s leadership in this area demonstrates how technological innovation, strategic collaboration, and a long-term vision can come together to create impactful change—one recycled part at a time.