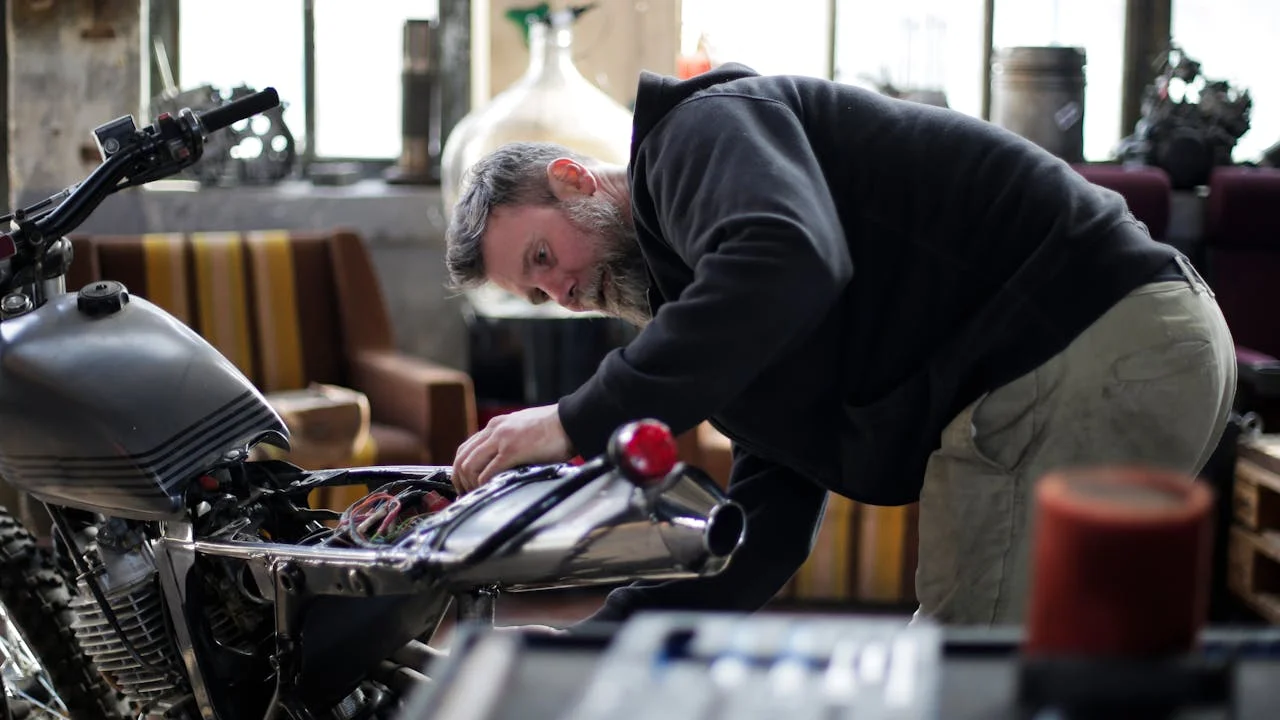
UL Solutions, a prominent figure in applied safety science, has just unveiled its latest endeavor: the inauguration of a cutting-edge Battery Enclosure Material Screening (BEMS) laboratory in Ise City, Mie Prefecture, Japan. This state-of-the-art facility is poised to support automotive manufacturers and their suppliers in evaluating and enhancing the performance of diverse materials within a secure environment, ultimately fortifying the safety of electric vehicle (EV) batteries.
The significance of battery enclosures in safeguarding EV passengers cannot be overstated, with the choice of materials playing a pivotal role in mitigating risks during battery-related incidents such as fires or thermal runaway events. The establishment of the UL Solutions Ise BEMS laboratory marks the company’s second facility worldwide, dedicated to screening and testing battery casing materials, following its flagship headquarters in Northbrook, Illinois. Anticipated to cater to regional clientele, this facility is set to expedite the development of robust battery enclosures, thereby ushering safer EV batteries into the market.
Hidehiko Yamajo, the regional vice president of UL Solutions Japan, emphasized the strategic imperative behind such initiatives, stating, “To extend the range of electric vehicles and remain competitive, automakers are investing in the development of lighter batteries and putting passenger safety as their top priority.”
With electric vehicle batteries enveloping the entirety of vehicle chassis, the resilience of battery casing materials under duress is of paramount importance. UL Solutions’ BEMS laboratory employs rigorous evaluations, aligned with UL 2596 standards, to gauge the performance of these materials under extreme conditions, including thermal runaway scenarios. Thermal runaway, a phenomenon triggered by critical internal battery temperatures, can culminate in fire outbreaks, smoke emissions, and perilous temperature spikes. Through the application of UL Solutions’ Battery Enclosure Thermal Runaway (BETR) assessments and the Torch and Grit (TaG) testing method, the new laboratory is poised to facilitate the automotive industry in fortifying passenger safety.
The BETR evaluation methodology, tailored to simulate thermal runaway incidents, scrutinizes the performance of both material patches and complete battery elements, notably reducing testing overheads and expediting development cycles for resin manufacturers and material suppliers. Meanwhile, the TaG testing methodology replicates the high temperatures and mechanical stresses characteristic of thermal runaway events, enabling a comparative ranking of battery casing materials.
In line with UL Solutions’ broader vision to expand its footprint in mobile and new energy technology domains within Japan, the inauguration of the Ise laboratory represents a significant milestone. Situated within the sprawling Ise campus, renowned for its diverse array of laboratories encompassing safety, electromagnetic compatibility (EMC), reliability testing, and large mobile devices, this facility underscores UL Solutions’ commitment to advancing safety standards in the realm of electric vehicles.
For further insights into UL Solutions’ battery enclosure material screening services, interested parties are encouraged to explore the comprehensive offerings provided by this pioneering entity.